Traders Hill Farm Talks Aquaponics and Tech
Unlock Deeper Agricultural Insights with CEAg World Insights
For any kind of CEA operation, thorough evaluation of new technology informs decisions that ultimately impact food safety, crop quality, and yields. When the technology relates to aquaponics production, considerations arise related to horticulture and aquaculture.
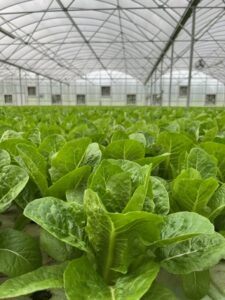
Romaine lettuce growing at Traders Hill Farm. | Photo: Traders Hill Farm
At aquaponics grower Traders Hill Farm in Hilliard, Florida, tech decisions are influenced by an approach in sharp contrast to the idea that aquaponics is a 50-50 revenue stream of fish and produce.
President and General Manager Tracy Nazzaro explained, “We use our fish very specifically to provide the nutrients for my plants. … We have found that we need far less fish to grow our plants than we originally contemplated, than what’s in published literature. So, we are a produce grower. We use aquaponics, and I like aquaponics, but my fish are not a revenue source for me.”
Nazzaro’s perspective reframes the growing process, including the labor and the technology it takes to make Traders Hill Farm (THF) run.
Designed with food safety first and foremost, as evidenced by its SQF (Safe Quality Food) certification, the facility has 52,000 square feet under cover with 32,000 square feet growing lettuce. With romaine as the flagship product, the farm has 100,000 plants growing in various stages 365 days a year.
The aquaculture operation and the system that converts fish waste into usable plant nutrients are separated from the produce operation. The only link is approximately 350,000 gallons of nutrient-rich water continuously flowing under the plants and recirculating back to the fish.
Approaching New Technology
Nazzaro shared that THF approaches new technology slowly and deliberately from an engineering standpoint — made easier by the fact her business partner, Dick Blaudow, is an engineer.
As an example, all harvesting is currently done by hand. “It is our intention to automate some of those processes, but we’re working through making sure that everything that we’re doing by hand is the exact way that we would want to automate it,” Nazzaro said.
With the farm’s design, she benefits from three separate systems, which allows the farm to confine trials to one system at a time. She’s currently testing a new filtration system in hopes of filtering finer particles, increasing water quality, and decreasing general cleaning needs.
“We’ll run it for about six months to a year to make sure we’re really happy with it before we would make the capital investment on adding other filtration systems in,” Nazzaro said. If they’re not happy, they can pivot and choose a different filtration mechanism for the other systems.
“When we implement technologies or methodologies or new systems, we really need to make sure that they’re going to work,” Nazzaro stressed. “We really have to make sure that we’re getting the financial return, so we always start small. We don’t do anything on the quick.”
Evaluating Potential Partners
Nazzaro shared that THF often gets calls from vendors with big promises. “So we have a really rigorous process of researching technologies, implementing technologies on a small scale, and working with companies that are going to provide us with service,” she said.
She pointed to Moleaer nanobubble technology, currently being trialed at THF. “The nanobubbler technology is something that I have been very intrigued with, and I actually heard about it through another company who came and gave me a demo. But they weren’t very professional, and they didn’t have real data to back up all the claims that they were making,” she explained.
In contrast, she shared that Moleaer has already been physically on site three times — with initial recommendations, at install, and again at midtrial — working closely with the team as they work through small-scale trials and then scale up.
“When we look at working with technology providers, having those knowledgeable team members on their side to work with my team members has been invaluable,” Nazzaro said. A similar six-month trial is underway with new lights from several manufacturers for the indoor vertical grow where THF plants start from seed.
“Everything we do, we kind of tiptoe into it,” Nazzaro added. “We have a pretty aggressive growth plan. So, as we build larger facilities and we work with our suppliers, they might initially think we could be a small customer. I’ll become a very big customer, probably rather quickly.”
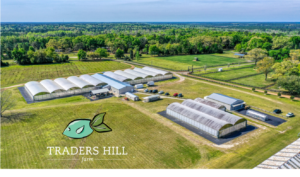
For Traders Hill Farm, choosing the right ag tech is a rigorous process. | Photo: Traders Hill Farm
Making the THF Tech Cut
Depending on the technology involved, Nazzaro uses specific criteria to evaluate the tech compared to its peers and decide what makes the cut. Using the nanobubble generator as an example again, Nazzaro explained the current trial compares two pools, each containing 10,000 plants planted at the same time.
Some of the criteria driving eventual decisions about Moleaer’s technology include improvements in time to maturity, plant weight, plant health, water quality, pathogen tests, root health, and dissolved oxygen levels. A horticulture tech manages all the data for every harvest. At the end of six months, there’s full data on comparative performance.
“Then we can get down to dollars and cents,” Nazzaro explained. “If it grew faster, if it weighed more, what is that economic value? Is it 10%? Is it 15%? Then we can sit down and say, okay, we roll this out to our whole facility, we would expect to see this type of an increase.” The same process applies to every piece of new tech THF implements.
For growers considering entering aquaponics and exploring technology, Nazzaro offered this advice: “Starting off, especially if you’re doing a new build, think food safety first. The first of that would be making sure that your aquaculture operation is very separate from your horticultural operation. That’s really key.”
She also emphasized that aquaponics is “not a crock pot” you can set and forget. It needs to be actively managed, with food safety the utmost concern. “I don’t think you can be too steadfast on food safety,” she added. “Going over and above, you can never go wrong.”