Choosing the Right Tech at Better Future Farms
In February 2023, Better Future Farms (BFF) broke ground on its first greenhouse facility. Located on 61 acres in Louisa County, Virginia, the 14.5-acre facility’s opening has become one of the CEA industry‘s most highly anticipated events. Part of the excitement revolves around the project’s technology, from its highly automated 10-acre production area and massive pack line to the other components that make this lettuce production facility tick.
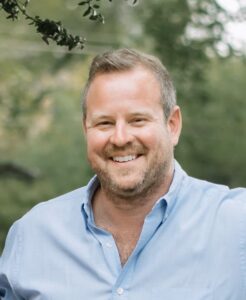
John McMahon, Co-Founder and COO of Better Future Farms | Photo: Better Future Farms
For co-founder John McMahon, BFF Chief Operating Officer, the greenhouse has been a dream come true of sorts. Prior to launching BFF with co-founder David Drescher, McMahon was well known in CEA circles as the founder and head grower of Schuyler Greens Company, a small-scale Virginia facility lauded for early adoption of cutting-edge technology and premium year-round lettuce.
As the new facility quickly approaches its official launch, McMahon said he’s humbled and grateful for where he finds himself.
“I can’t believe I get to work here,” he said.
Part of that feeling stems from the technology he and the team have implemented in the new facility and its impact on streamlining processes and making BFF a better place for its employees.
Matching the Level of Technology to the Facility
McMahon said long-term sustainability is essential for any CEA business. That achievement requires matching the levels of both investment and technology to your crop. The latest high-tech equipment isn’t appropriate for every project. Determining what’s right and what isn’t takes work.
For BFF, McMahon said, “It was definitely an iterative process. We met with a lot of different technology providers around the world and explored new technologies and existing technologies, both high-tech and low-tech.”
One step, he said, is simply breaking down the flow of your greenhouse process, whether you grow bedding plants or lettuce. Then you can figure out where it really makes sense to add automation or higher technology. Another consideration, especially with new technology, is whether it’s ready for prime time — which, in BFF’s case, means large-scale commercial production.
He noted that there are many companies working on autonomous growing technology, for example, that have done a great job in small-scale facilities or small-scale greenhouse trials. But they haven’t been proven at a large-scale facility.
“You have to assess the risks. If you’re doing something in a small trial area, it’s not a huge deal. But when you’re doing it on a large commercial/industrial scale and your algorithm is wrong, it can cost you hundreds of thousands of dollars or more,” he said. “So, it’s combining technology, assessing the risk of where that technology is in the development curve, and then trying to apply it in the most intelligent or cost-effective way possible.”
McMahon pointed to transplanters with machine vision as another example of matching and balancing technology to your project.
“Ultimately, if you still need an operator at that transplanter, you have to ask if it makes sense to spend additional money on that capability if you’re still going to need someone to operate and monitor the piece of equipment,” he said.
Balancing the Variables That Impact Tech Decisions
When considering CEA technologies, McMahon confirmed that budget is always a primary factor. Geography and climate also have a huge impact on what type of technology makes sense. Also, the cost of controlling the CEA environment, whether through heating, cooling or dehumidification, necessitates yields that cover the additional cost.
Many other factors also come into play. For McMahon and the BFF team, labor is a crucial variable — not only its availability, but also the likelihood that available labor would want to do certain jobs.
“I have transplanted so much lettuce by hand over the years, I know what that’s like. I know I wouldn’t want to do that the rest of my life, and I know a normal person wouldn’t want to either,” he explained. “So, it’s trying to remove the very rote, repetitive things that people wouldn’t want to do eight hours a day. Greenhouses can be very repetitive.”
While any decision must make economic sense, McMahon said you have to see the bigger picture.
“It might cost more money to automate some things, but if it makes your employees happier or have a longer tenure with your company — less turnover, less stress, more engaging work versus just repetitively doing the same action over and over again — I think it’s a no-brainer,” he said.
He emphasized there’s no downplaying the fact that working in a greenhouse is hard work: “It’s physical and, as much technology as we have, it’s still a type of farming. So that environment also drives some of the automation, trying to remove people from an environment that’s not always hospitable or comfortable.”
He recalled many holidays at Schuyler Greens, transplanting lettuce by himself so employees could have the day off.
“Doing that, it was not hard to say that [BFF] needed to invest in either automated transplanting or automated seeding or whatever — things that I couldn’t do or couldn’t afford to do on a very small scale,” he said. “I understood that if we’re going to be sustainable on a larger scale, we needed to have those. I have a lot of empathy for my employees.”
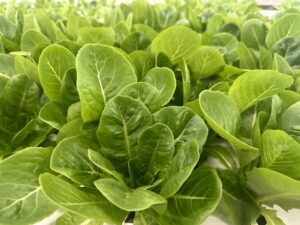
Romaine Lettuce Grown at Better Future Farms | Photo: Better Future Farms
Finding the Right Partners for the Journey
McMahon, whose pre-CEA background includes an MBA in finance and extensive corporate experience, shared that he and Drescher focused on finding partners to complement their strengths and help their vision for BFF come to fruition, including its technology. Securing funding from Generate Capital, a leading sustainable infrastructure investment and operating platform, has been a key component in the process.
Unlike more speculative venture capitalists, McMahon explained that Generate is very risk averse, focusing on large capital projects and longer-term time horizons.
“They really want to make sure whatever technology we’re using, it’s been vetted, it’s been pressure tested, and it can work and work every day,” he said.
The scenario is very different from when McMahon operated Schuyler and had more flexibility to take risks, both because of the smaller scale and the lack of large outside investors. He underscored the idea of matching technology to your project — including its investors.
Technology implemented in BFF’s first greenhouse minimizes risks that large-scale production presents.
“With all this technology in general, whether it’s automation or software packing or warehouse stuff, whenever there’s machines and software, there’s always hiccups or kinks,” he said. “Usually, the first mover has to work out a lot of those things. So sometimes you’re better to be the second or third mover.”
With Generate, whose reputation includes a sustainability emphasis, McMahon said their investment goes beyond caring about things like capturing rainwater for irrigation or using renewable energies at the BFF facility.
“Even with labor and automation, they really want to be part of a sustainable business, not just funding a business that’s trying to get cheap labor and burning through people,” he said. “They genuinely care about making the business stable in all areas.”
Anticipating Opening Day
McMahon said his growing background has been integral to success: “I wouldn’t be in the position I’m in now if I hadn’t gone through 10 years of hands-on growing. It has helped decipher what’s noise or what’s really important.”
At the time of this interview, lettuce is in the greenhouse, the team is calibrating systems, and they’re working on “the last 2%.”
While the phrase “state of the art” is thrown around a lot in CEA, early reports indicate the BFF facility lives up to the label. McMahon, who avoids anything close to boasting, said the semi-closed Van der Hoeven greenhouse has some of the most sophisticated systems in existence.
“We have a ton of advisors all around the world that either work for us or for Generate to make sure the project’s going on plan through the construction,” McMahon said. “Generally, the comment is that you’ll see bits and pieces of this in different facilities around the world, but you rarely see all the different systems under one roof.”
While he prefers not to divulge many specifics, he mentioned irrigation, filtration, growing systems, automated seeding, automated transplanting, automated harvesting, and the largest automated pack line he’s ever seen in a greenhouse.
“At this point, it is probably the most advanced lettuce greenhouse I’m aware of, which is cool,” McMahon said. “But ultimately, we’ve got to grow lettuce. It’s a tool, a sophisticated tool. It’s our job to leverage that tool to make us as competitive as possible with field-grown lettuce.”
He reiterated that he’s humbled by what has transpired so far.
“I can’t believe, after all the blood, sweat, and tears, that we were able to build and bring this to life,” he said. “To see it from an idea into now seeing it in operation, and all the teams of people that brought this project to life — it’s not just me. It’s not my business partner, David. It’s way beyond us.”
McMahon expects BFF’s first commercial sales to happen in July 2024. Lettuce produced at the new facility will be sold under Taylor Farms’ Earthbound Farm organic/greenhouse brand.