Bell Peppers Get an Ag Tech Boost at Twin Creeks Greenhouse
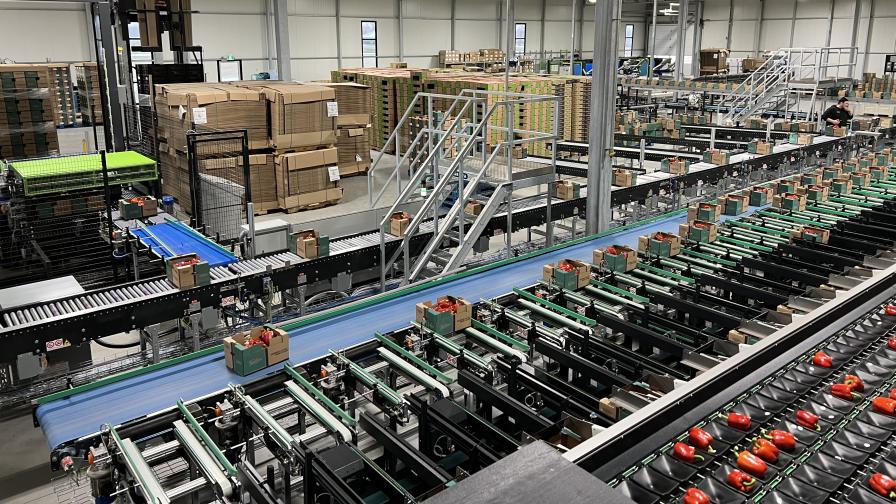
The new pack line at Twin Creeks Greenhouse doubled the output with the same amount of labor.
Photo courtesy of Twin Creeks Greenhouse Inc.
When Mike Cornelissen started growing greenhouse bell peppers in 2016, he had no direct greenhouse experience. But he did have strong agricultural connections and an affinity for early adoption of technology. Twin Creeks Greenhouse launched with 10 acres in production and what Cornelissen considers fairly standard automation for the time: basic pack lines and climate controls comparable to its competitors.
Though more automation was planned, Cornelissen and Danielle, his wife and co-owner, didn’t foresee the level of technology that would be in play at the Ontario greenhouse. Today, the family-owned and -operated company grows 40 acres of hydroponic red, yellow and orange bell peppers under glass. From an enhanced-accuracy packing line to autonomous picking carts, the automation at Twin Creeks Greenhouse is no longer standard.
“We went a lot further with the automation than we were expecting when we first built,” Cornelissen said. “That came after a few trips to the Netherlands. Obviously, the technology has changed over the years as well.”
Expansion = Automation Inspiration
It didn’t take long for Twin Creeks Greenhouse to expand from 10 acres to 20, but automation wasn’t a big component in that first expansion, which focused more on infrastructure. Once they had 20 acres in CEA bell pepper production, the team started exploring automation more.
“We did a lot of research into the automation and that kind of pushed us to go to 40 acres,” Cornelissen said. “We saw that the automation cost was going to be the same if we grew at 20 acres or 40 acres, so the return on investment made more sense to go to 40 acres.” As a result, a 20-acre expansion and a major investment in automation went hand-in-hand.
Around the same time, the minimum wage in Ontario went up dramatically. The impact was significant in an industry with many employees at that wage level. Automation at Twin Creeks Greenhouse advanced rapidly from 2016 to 2020.
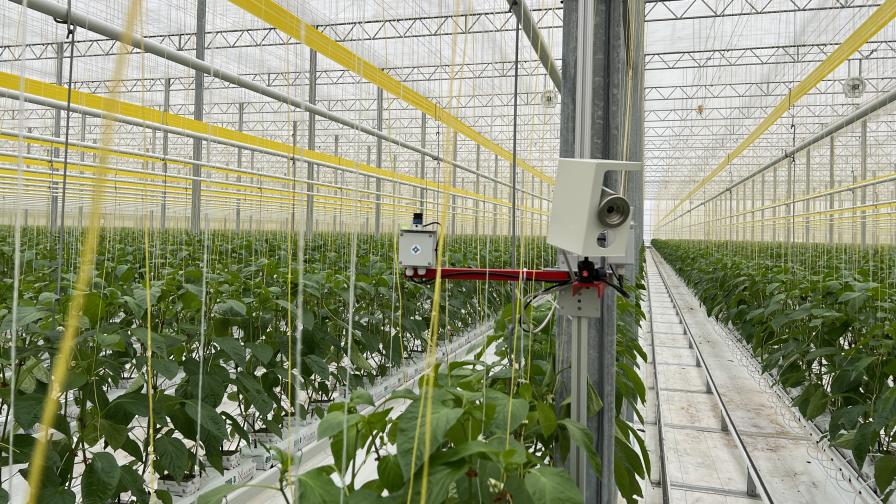
Updated climate control systems monitor the greenhouse and incorporate intelligent algorithms in data analysis.
Photo courtesy of Twin Creeks Greenhouse Inc,
Packing Line Priorities
Twin Creek’s automation started with a new pack line complete with palletizers and accu-fill capabilities.
“Basically, our pack line that did 20 acres and our new pack line that does 40 acres use the same amount of labor, but the new line has doubled the output,” Cornelissen said.
He estimated that having palletizers saves one to two employees, plus he gets better-stacked skids. While he said the payback isn’t ideal, the equipment is well-built and runs smoothly. Improving accuracy on packing weights was another major step.
“With most things in produce, there are minimum weights on everything. You don’t want to give away any extra weight,” he said. “With our new pack line, it’s quite long to allow us to more accurately fill our boxes. […] So, we’re gaining yield by getting our box weighed more accurately.”
Installed in 2021, the pack line got a major upgrade in 2022 with the addition of camera technology for sorting. This included cameras for external grading as well as a camera that scans peppers for internal defects that can’t be seen on the surface. While they’re still tweaking the technology, Cornelissen hopes that sorting with the cameras can streamline sorting, which now requires 10 people on the sorting table. The quality of peppers packed has also improved.
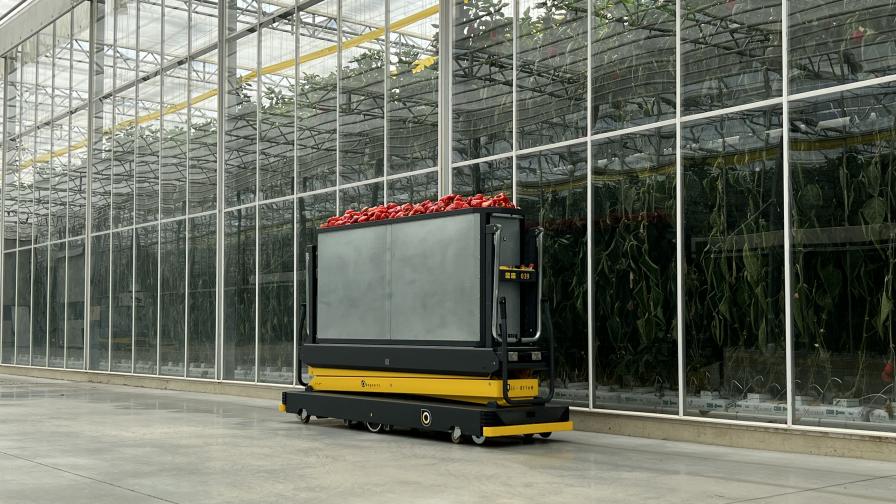
Pick carts at Twin Creeks Greenhouse all operate independently, keeping the pack line supplied without delays.
Photo courtesy of Twin Creeks Greenhouse Inc.
Individual Automated Picking Carts
Cornelissen had an Aha! moment on a Netherlands visit when he saw automated ATV picking carts in action.
“When I had first seen it online, I wasn’t that intrigued. But when I saw it in person, it really started making sense to me that’s the way we had to go,” he recalled.
While it’s not uncommon for greenhouses to have ATV carts, it usually involves one automated vehicle pulling a train of eight or nine carts — as Cornelissen originally planned. But at Twin Creeks Greenhouse, all the carts are automated. With their picking bin on top, each one operates individually, so there’s no hitching, re-hitching or delays. When a worker finishes their cart, another one is waiting for them and the finished cart is on its way to the pack line.
The impact on efficiency is significant.
“It’s just the flow of the crop and having that buffer in front of your pipeline to keep it able to run all the time,” he said. “Our pack line basically takes the same amount of labor if it’s running full speed or half speed. So, it’s very important we try to keep it running.”
The choice to go fully automated on the picking carts required a much larger investment.
“With the other rig, you only need maybe four units. Six at most,” Cornelissen said. “But in our case, we have 64, so that really increased the costs.”
2021 was the first operating year for the carts, and it’ll be a few more years before they’ve paid for themselves.
“It wasn’t that quick of a return on investment,” he said. “But one thing we do, we look at the long-term goal, not always the short-term. We wanted to do it right from the beginning, not regret it down the road.”
Ongoing Automation Advances
In addition to the pack line and pick cart advances, automation at Twin Creeks Greenhouse improves the growing environment and the growing itself. Last year, the company did a major upgrade of its climate control system, switching to a new system offering intelligent algorithms.
“It’s kind of like their AI, but they call it intelligent algorithms, which is a more accurate way of defining the system,” Cornelissen explained. “It’s allowing us to hopefully better manage our climate and lower input costs while increasing yields.”
Automated climate controls were phased in throughout the operation to automatically adjust the greenhouse climate every five minutes, constantly fine-tuning environmental conditions based on forecasts, actual conditions, and settings input by the Twin Creeks team.
“It’s not just learning the system. It’s learning different growing ideas, so there’s a little bit to it,” he said. “We’re very excited and happy with what we’re seeing. But we want to take our time to work our way into it.”
The company also utilizes targeted technologies to collect images and data for CO2, humidity, temperature and light to help identify issues in the greenhouse and forecast production for the current week.
“We work with a lot of different partners. So they can also look at our crop visually and basically go on a crop walk from their office, wherever they are in the world,” he said. Other technology takes air samples that help identify conditions that favor problems such as powdery mildew, for example, long before scouts see it. Early detection allows more efficient, effective and bio-friendly interventions.
Lessons to Leverage and Learn
The automation at Twin Creeks Greenhouse does more than save on labor.
“Basically, everything I have either increases the quality of the product we’re selling plus the labor savings, or it increases yields plus the labor savings,” Cornelissen said.
Including office staff, Twin Creeks Greenhouse operates with about 60 people. Without automation, they’d need around 10 more. But there are some drawbacks.
“With better automation, like our packing system, it is very focused on bell peppers. If we had to switch our crop, our system doesn’t adapt well and would struggle. Some less automated systems can adapt a little bit better between different crops,” he said. “When you get more automated, it can make you a little bit more specialized, which is fine, but then it’s a lot harder sometimes to change.”
For Cornelissen, who spoke to CEAg World from a tractor while planting soybeans, being family-owned and -run plays a big part in automation, too.
“My wife and I run the company. We’re a very nimble operation, so that does allow us to adopt this technology a little bit quicker sometimes, because we’re a little bit more hands-on. And when we agree on it, we pretty well move ahead with it,” Cornelissen said. “I grew up on a farm and my dad’s always been an early adopter of technology, so I guess that’s how I grew up. It’s part of the way we farm.”
This article is part of our inaugural edition of CEAg World Insights. Click here to view the entire interactive report.